刀具是机床的重要组成部分,直接执行生产加工任务,是完成零部件加工的重要工具。从刀具材料的选择,到刀具的装配再到刀具的使用,都与加工质量和加工精度紧密相关。
在加工制造业飞速发展的今天,各种新材料、新工艺层出不穷,刀具的材料和工艺也在不断的变化更新中。面临日益提高的加工要求,如何正确使用刀具,使刀具与机床的匹配更加优化,更好的配合完成生产加工任务,是现代
机械加工领域普遍关心的重要问题。
1.刀具使用的基本耍求
刀具与机床之间是相互依存的关系,没有刀具的机床是不完整的,机床又是刀具加工工件的载体。刀具使用的基本要求不仅仅是要与安装的基础相匹配,同时也要与被加工工件相匹配。外形的匹配、尺寸的匹配是刀具能够安装在机床上的基础条件,
但这只是基础的一部分,更重要的是机床安装刀具是要利用刀具完成特定的加工任务的。而在执行加工任务的过程中,刀具不仅仅要保证工件加工的及高难度,更要对切削力、切削扭矩、切削热度能够承受、传递和导出,这是刀具所应该具有的基本性能。
刀具与被加工工件之间的匹配包含较多的内容。其中刀尖是刀具的重要部分,是刀具与工件接触的常用点位,也是重要的点位。刀尖的切削性能受三方面因素的影响,即基体材料特性、刀尖表面形状以及刀尖的几何形状。
三者之间配合的程度决定了它们之间交互作用的大小,进而决定了刀尖的性能。基体材料承受着加工过程中大部分的切削力和热度。现今基体材料分为多种类型,其中应用频率较高的为硬质合金。以钨基硬质合金为例,钨钴类硬质合金中,基体含钴量越高,
抗冲击能力就越强。而基体含碳化钨等硬质向越多,其硬度也就越高。也正是因为基体材料的特性在加工中,如果冲击较小,则可选用基体材料含钴较少的硬质合金的刀具,这种刀具会有良好的耐磨性。如果冲击较大,则可选用基体材料中含钴量较高的硬质合金的刀具,
这种刀具硬度高,可有效防止加工过程中出现崩刀的状况。
在机械加工中正确的使用刀具不仅可提高生产加工效率还保证了工件在加工中的精度。
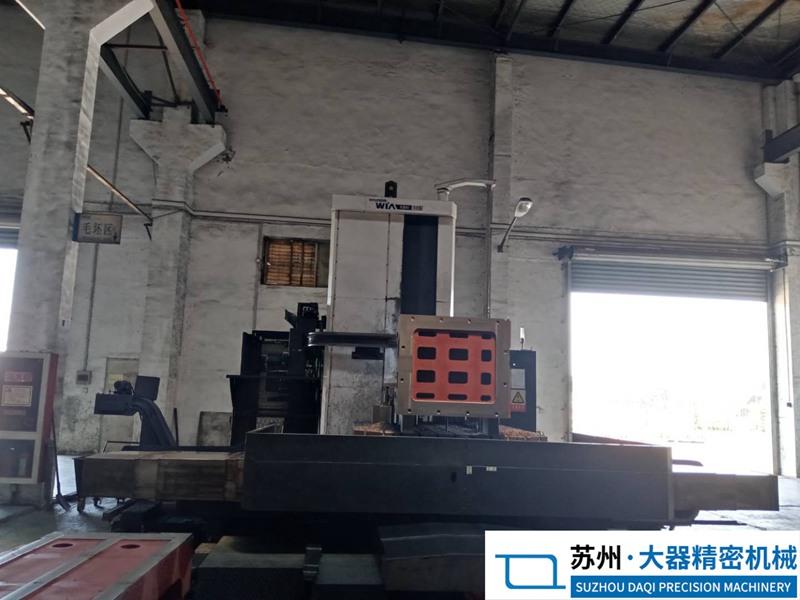